Polymer Nation Flooring FAQ | Expert Guidance on Coatings & Installation
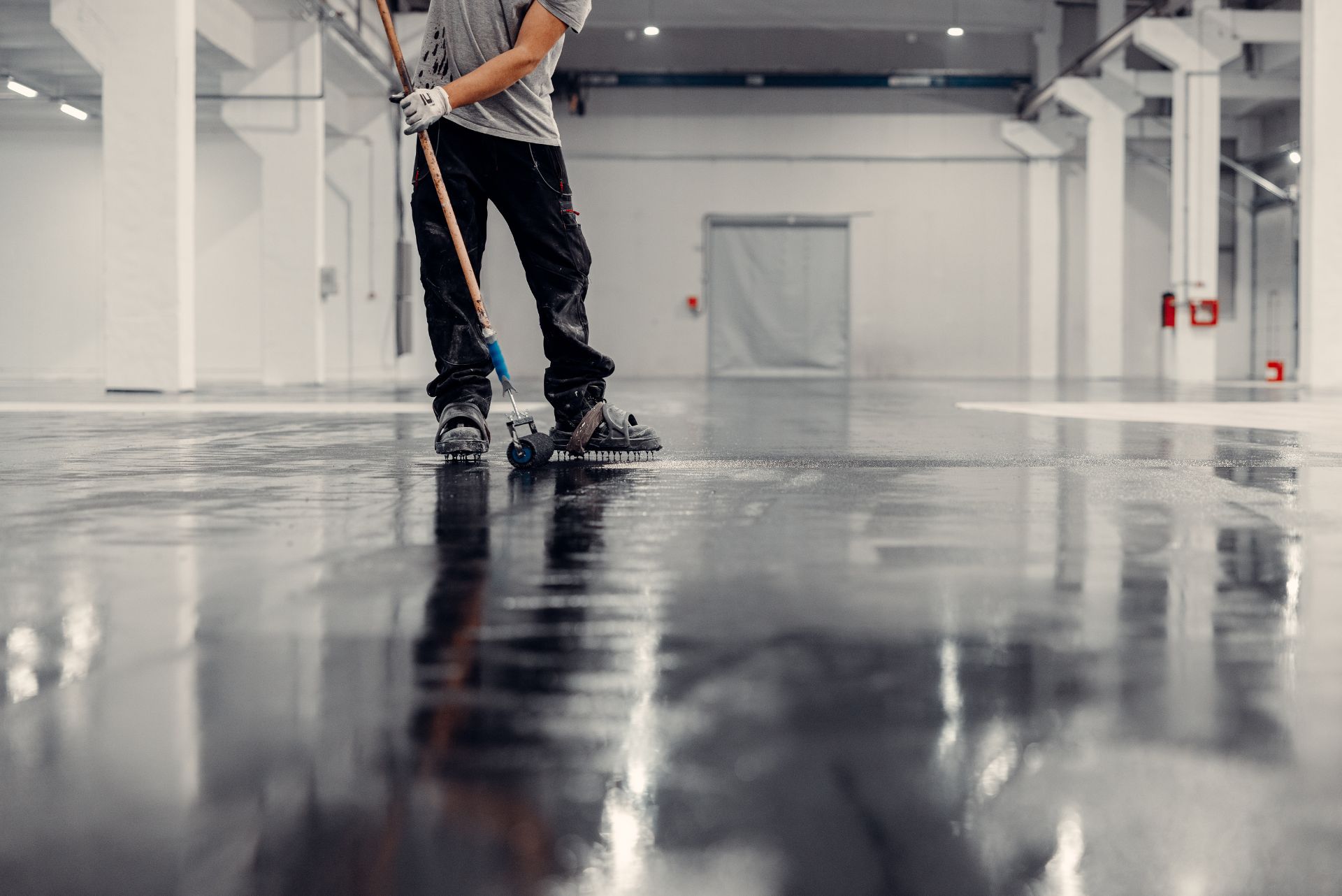
Moisture & Concrete Substrates
FAQ
Get answers to common questions about Polymer Nation flooring solutions, including moisture testing, coating adhesion, surface preparation, and troubleshooting gloss, color, and finish issues.
ASTM D 4263 (Plastic Sheet Method) – Identifies surface moisture but lacks quantitative accuracy.
Moisture Meters – Measures comparative moisture levels up to 2 inches deep but does not provide precise results.
ASTM F-1869 (Calcium Chloride Test) – Measures moisture emission rates but only at the surface level.
ASTM F 2170 (Relative Humidity Test) – Provides deeper slab moisture readings and is more reliable for determining actual moisture content.
Surface Preparation & Coating Adhesion
FAQ
Get answers to common questions about Polymer Nation flooring solutions, including moisture testing, coating adhesion, surface preparation, and troubleshooting gloss, color, and finish issues.
Gloss, Finish, & Color Issues
FAQ
Get answers to common questions about Polymer Nation flooring solutions, including moisture testing, coating adhesion, surface preparation, and troubleshooting gloss, color, and finish issues.
Incomplete mixing of colorants before adding the hardener.
Different batch numbers of colorants leading to variations.
UV exposure causing color shifts over time.
Common Coating Defects & Repairs
FAQ
Get answers to common questions about Polymer Nation flooring solutions, including moisture testing, coating adhesion, surface preparation, and troubleshooting gloss, color, and finish issues.
Excess solvent use during mixing.
Application over incompatible surfaces or high temperatures before curing.
Cold substrate temperatures causing contraction during curing.
Improper mixing of resin and hardener leading to weak curing.
Poor maintenance practices, such as neglecting regular cleaning.
Soft concrete substrates, which reduce coating performance.
Application & Maintenance Best Practices
FAQ
Get answers to common questions about Polymer Nation flooring solutions, including moisture testing, coating adhesion, surface preparation, and troubleshooting gloss, color, and finish issues.
For widespread issues, remove the entire system and reapply from a clean substrate.
For smaller areas, remove the damaged section, prepare the surface, and patch with the same coating system.
Lint from roller sleeves – Always use lint-free rollers.
Inadequate surface cleaning – Ensure proper dust and debris removal.
Poorly mixed additives – Thoroughly blend dry additives before application.
Frozen product usage – Always store coatings above freezing temperatures.